What is Kanban?
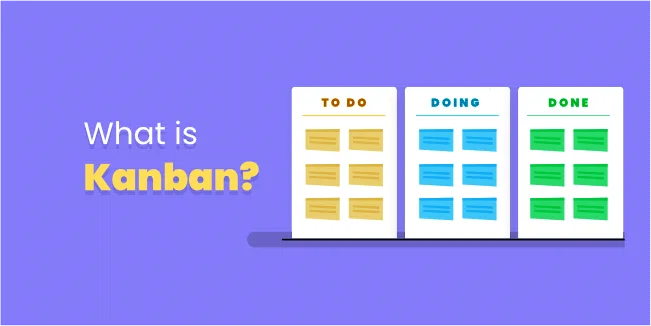
As a software development company, we know that every software development project should proceed according to a predetermined software development plan, the main core of which should be the Software Development Life Cycle.
However, it is worth remembering that even the best process requires constant improvement. It is because we operate in a constantly changing environment, and change is a natural part of every aspect of our lives. That is why it is worth preparing for each change, and processes that help organize reality and affect efficiency are helpful.
The purpose of using the Kanban method is to increase the efficiency of business processes and shorten the time of product delivery by constantly improving and streamlining the system. And all this is to achieve the highest possible efficiency in implementing tasks. In turn, efficiency has a crucial impact on the duration of the project and its costs.
Our experience to date and a wide portfolio of successful projects prove it is worth implementing this method in software development projects.
A few words about Kanban
Kanban is a visual approach to managing work through a process. Kanban shows the process (workflow) and the actual work being done as part of that process using a visual system. Kanban aims to identify potential bottlenecks in your procedure and correct them so work can flow efficiently at a high throughput rate. Importantly, Kanban is a project management tool based on the Agile methodology.
History of Kanban

It all began in the early 1940s when Taiichi Ohno (an industrial engineer and entrepreneur) created the first Kanban system for Toyota automobiles in Japan. It was designed as a basic planning framework to optimize production at every stage by effectively controlling and managing work and inventory. Toyota was having difficulty keeping up with American automobile companies regarding productivity and efficiency. Toyota used Kanban to create a flexible, efficient just-in-time production control system that increased productivity while decreasing expensive inventory of raw materials, semi-finished materials, and completed products.
A Kanban system should ideally span the whole value chain, from supplier to consumer. It assists in preventing product shortages at different stages of the manufacturing process by keeping track of all stages of production. The need for continual monitoring of the process is inherent with Kanban. Specific attention must be paid to prevent bottlenecks that might jam the manufacturing process.
Kanban has been adapted for other business areas, including software development and marketing. For example, in software development, a Kanban board is used to track the progress of tasks and keep developers informed about what needs to be done next. The different columns on the board might represent different stages of development, such as "requirements," "design," "coding," and "testing."
What is the Kanban Method?
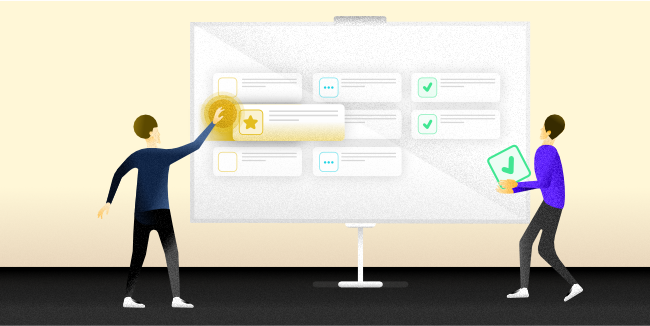
In the year 2004, David J. Anderson was the first to apply the concept of Kanban to IT, software development, and knowledge work in general, inspired by Taiichi Ohno's ideas in the manufacturing sector. David expanded on the work of Taiichi Ohno, Eli Goldratt, Edward Demmings, Peter Drucker, and others to create the Kanban Method. Pull systems, queuing theory, and flow are all concepts he added to the literature. His first book about Kanban — "Kanban: Successfully Evolutionary Change for your Technology Business," was published in 2010.
The goal of the Kanban Method is to improve whatever you do gradually – whether it's software development, Human Resources, Marketing, or Sales. Applying Kanban Principles to almost any business function can provide significant benefits.
What is a Kanban Board?
Before we go any further, let's clarify what we mean by Kanban boards and cards.
Consider a whiteboard divided into vertical lanes, with each lane representing a stage in your process. The far left lane usually contains work items that have yet to be started, and the far right lane holds work items that have been completed. In Kanban, work begins on the left side of the board and progresses towards the right: Work items that have not yet been started are put into a backlog. Those that have been created but not completed move to the "in progress" column, and those that have been completed go into a separate "completed" column.
Product Backlog ("To Do") – The board section where items enter your process from the leftmost lane. The backlog is for items that have not yet been started.
In Progress (Doing) – The board section where work started is located. It is the column in which work should be actively moving towards completion.
Completed (Done) – The board section where completed work goes. Work should move from the rightmost "completed" lane to the "in progress" lane as new work is started.
Kanban boards can also show you information about your procedure beyond just the visualizing of phases. Two examples are process standards (codes for using the board) and work-in-progress limits.
What are Kanban Cards?
In Kanban, work items are represented by cards. These might be compared to sticky notes on a whiteboard. Many organizations begin by using a physical Kanban board that reflects their existing process. Each kanban card, or sticky note, represents one job item.
Kanban principles
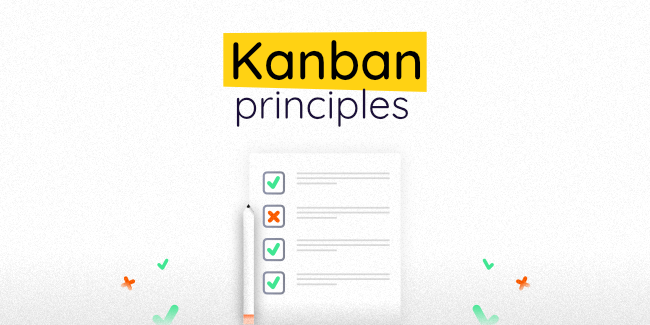
The above explanation of Kanban boards and cards is quite basic, demonstrating how these tools are used. You may envision nearly any procedure, at any level of your company, by moving cards from left to right through defined phases in a process and providing information on the cards.
Kanban is quite flexible, but there are certain fundamental Kanban principles and methods that will assist you in reaching your objectives. We'll go through them for you.
Visualize work
You can follow the flow of work through the Kanban system by drawing a visual model of your job and process. Making work visible and visual indications of obstructions, bottlenecks, and queues increases communication and collaboration. It helps teams see where they should focus their efforts to increase flow.
It is the essential stage in adopting and implementing the Kanban Method. You must picture - either on an actual board or an electronic Kanban Board - the current process steps you use to deliver your work or service. Your Kanban board can be essential to complex, depending on the complexity of your process and work mix (the many sorts of work items you deal with and finish). After you have an image in mind for your procedure, you'll be able to see the current work that you're doing.
Limit work-in-process
You can speed up the movement of items through the Kanban system by restricting how much-unfinished work is in progress. You may also avoid issues caused by task switching and curb the necessity to reprioritize things constantly. WIP limits allow teams to achieve more significant results than ever before in a safer, more sustainable way.
Limiting work-in-progress (WIP) is critical to the success of Kanban, a "Pull" system. You encourage your team to finish current tasks before starting new work by limiting WIP. As a result, unfinished tasks must be finished and marked as completed. It creates system capacity, allowing new work to be pulled. According to Don Reinertsen, you may get started with no WIP limits and watch the initial work in progress as your team begins to use Kanban. Define WIP limitations for each workflow stage (each column of your Kanban board) at half the average WIP after acquiring enough data.
Typically, many teams limit WIP to 1.5 times the number of people working in a particular phase. Limiting WIP and limiting each column of the board's WIP limits helps team members finish what they're doing before moving on to new things and sends a message to the customer and other stakeholders that there is limited capacity. Cycle time defines the average time it takes to complete a task.
Focus on flow/manage flow
You may improve your Kanban system by applying work-in-process limitations and team-driven regulations, as demonstrated by these two organizations: You can use the following principles to optimize your Kanban system:
- Make improvements to the workflow
- To analyze the flow, collect data.
- Get a head start on identifying potential problems by monitoring these indicators.
It would help if you had a constant workstream to deliver faster and more dependably, which will benefit your clients, team, and company. A time- and money-saving Kanban benefit is the ability to spot areas for continuous improvement.
A Kanban system allows you to keep track of the flow of work by displaying the workflow's various phases and the status of labor in each stage. Depending on how well your process is defined and WIP Limits are implemented, you'll see either a smooth flow within WIP limits or work accumulating as something gets delayed and begins to clog up capacity. It all impacts how work travels from start to finish in a workflow (some refer to it as the value stream). Kanban aids your team in analyzing and modifying the system for tasks to move more swiftly through the process.
Continuous improvement
Once you've built your Kanban system, it becomes the foundation for a culture of continuous improvement. Teams keep track of their performance by monitoring flow, quality, productivity, lead times, and other variables. Experiments and analysis may alter the system to improve the team's performance. Continuous improvement is a Lean improvement method that minimizes time and money by streamlining processes throughout the company.
Start with what you are doing now
The goal of the Kanban Method isn't to make a major overhaul right away. On the current operation, Kanban should be implemented as soon as possible. Any required modifications can be introduced gradually over time, at a convenient pace for the team.
Initially, respect current roles, responsibilities, and job titles
Kanban is different from other approaches in that it does not necessitate any organizational changes on its own. As a result, you won't need to adjust to your existing job roles or responsibilities (for example, project managers or the development team), which may function effectively. To identify and implement any necessary changes, the team will work together. These three principles aid organizations in overcoming the typical.
Make Process Policies Explicit
7. Make Process Policies Explicit It's also essential to define and display explicitly, in this case, your policies (process rules or guidelines) for how you do the work you perform. You may accomplish any job in the system by developing clear process standards. The policies may be established at the board level, at a swim lane level, and in each column. They may be a list of steps to complete for each work item type, entry and exit criteria for each column, or anything else that aids team members in managing the board's flow of work. The most important thing to remember about explicit policies is that they must be specified clearly and presented visibly on the board, lane, and column.
Encourage acts of leadership at all levels
Kanban encourages continual improvement at all company levels, and it claims that leadership actions don't have to come from the top. People at all levels may contribute ideas and demonstrate leadership for changes to continuously improve their product or service delivery.
Implement Feedback Loops
Feedback loops are an essential feature of any effective system. The Kanban Method pushes and supports you in establishing a variety of feedback loops: including review stages in your Kanban board process, measures, and reports, as well as various visual cues that give you real-time feedback on progress or lack thereof in your system. Getting feedback quickly, especially if you are off track with your work, is critical to accomplishing the right product or service to the customer in the shortest amount of time. Feedback loops are essential for this.
What is Kanban Used For?
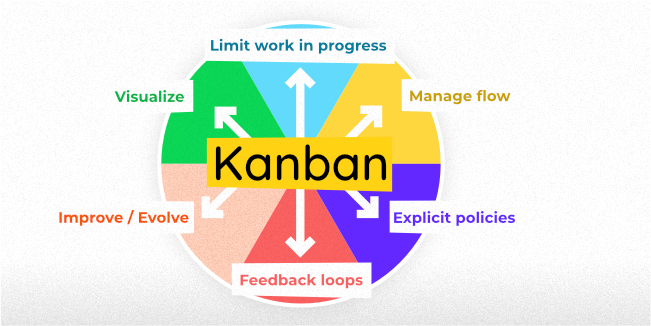
Like most knowledge workers, you've probably already been overloaded with well-intentioned solutions that make things more difficult. Consider the following questions: what is Kanban, and why should I care?
- Do you ever feel like you're constantly moving from one activity to the next, unable to focus on anything long enough to achieve success?
- Do you feel like you're always working but never as productive as you'd want to be?
- Is your team having difficulties with basic communication, resulting in a duplicate effort, defects, rework, and other problems?
Kanban may be the ideal solution if you have answered yes to these questions. Many knowledge workers encounter these difficulties and discover clarity and freedom using Kanban.
How does Kanban help?
Kanban transforms data that would otherwise be delivered via speech. Kanban enables you to better identify vital information by converting your "to-dos" into cards aboard. It creates a common location where everyone involved in the project may go to discover the most up-to-date information. When utilized correctly, Kanban can significantly lessen the number of time teams spend in meetings that only provide status updates. Teams may, rather than discussing work, spend more time doing it.
Kanban standardizes cues and improves procedures, allowing you to minimize waste and maximize value. You can see how your work progresses within your team's process to help you communicate status, but it also allows you to offer and acquire context for the job.
Benefits of Kanban methodology
- Minimization of labor without loss of efficiency
- Shortening the time of lead products, products, or services to the customer
- Quick responses to current needs
- Better adapting products and services to customer requirements and at the same time improving their quality
- Creating the entire information process
- All team members have direct access to each teacher or assignment
- Quick information on narrow services and system problems
- Reducing the costs of the company thanks to it, it constantly updates the system.
- Costs go down not only after implementing the methods, but all the time it is
- Easy and quick implementation of methods in almost any organizational department without any work involved
- According to the principles of "managing what you have," the industry or company department can implement it in the company
- A happier and more motivated team
Thanks to the implementation of Kanban, Toyota reduced shortages by as much as 95%, decreased the level of inventories by 75%, which consequently led to a 25% increase in production, a considerable reduction in production costs, and a significant increase in competitiveness.
How to implement Kanban?
There is no one-size-fits-all answer to this question, as the best way to implement Kanban will vary depending on the specific organization and context. However, there are a few general tips that can help get you started:
Start small: Don't try to overhaul your entire process at once – start with a small team or department and see how it goes.
Use visual boards: Make use of physical boards or electronic tools to visualize your workflow and track progress.
Encourage collaboration: Kanban is all about fostering collaboration between team members, so make sure everyone works together.
Focus on continuous improvement: A big part of Kanban and Lean Manufacturing, in general, is constantly working to improve your process and eliminate waste. Don't get discouraged if you don't get it right the first time!
Make metrics transparent: Try tying the metrics you use to track your progress (e.g., cycle time, lead time, throughput) to visual indicators on your Kanban board. It will make it easy for everyone to see how you're doing and where you need to improve.
Try a pilot project: If you're unsure if Kanban is suitable for your team or organization, start with a small pilot project. It will help you get a feel for how the process works and whether it's a good fit for you.
Use feedback to improve: As your team starts using Kanban, be sure to collect feedback and use it to improve the process continuously. It is an essential part of making Kanban work well for your team.
Celebrate successes: When your team achieves a goal or a task ahead of schedule, take the time to celebrate! It will help keep everyone motivated and working towards common objectives.
Evolve as needed: As your team and business change, your Kanban process will. Be prepared to evolve your process as is necessary to continue achieving results.
Summary
The Kanban system is more than a board with tasks on the wall. The easiest way to understand Kanban is to adopt its philosophy and apply it to daily work. It is the only way to know the power of this methodology.
When choosing a custom software development partner, make sure that he uses the Kanban system, which is an excellent tool for project management according to the Agile methodology. Only the best product development company is open to modern project management methods.
If you want to ensure that Kanban and Agile will facilitate your software development process, arrange a free consultation with us.